In the dynamic world of plastics, the art of enhancing polymer properties has evolved into a science thanks to the ingenuity of polymer additives. These specialized ingredients play a pivotal role in shaping the characteristics of plastic materials, making them more versatile and adaptable for a wide range of applications.
Defining Polymer Additives
It’s essential to grasp the fundamental significance of polymer additives in the plastic industry. Polymer additives are compounds added to plastic materials during various stages of manufacturing and processing. These additives bestow a multitude of enhancements upon polymers, elevating their properties and enabling them to meet specific performance criteria. In general, there are two major categories: processing aids and functional additives.
The Marvels of Polymer Processing Aids
The major types of polymer processing aids include the following:
1. Lubricants
Lubricants are a crucial group of processing aids that help ease the flow of polymer materials during manufacturing. They reduce friction between polymer molecules, making it easier to mold and shape plastics. This results in smoother processing and enhanced productivity, especially in industries that rely on extrusion and injection molding.
2. Heat Stabilizers
Plastic processing and molding involve heat generation from heating, friction, or shearing, potentially leading to the degradation of plastic products. In order to counteract this heat-induced deterioration and aging, a heat stabilizer is introduced to prevent the plastic from decomposing or altering under elevated temperatures.
3. Foaming Agents
Foaming agents introduce tiny gas bubbles into polymers, creating a cellular structure that reduces material density. This lowers the overall weight of the plastic, making it an ideal choice for applications where weight reduction is crucial, such as in the construction of lightweight automotive parts.
Exploring the World of Polymer Functional Additives
Some of the primary categories of polymer functional additives are as follows:
1. Antioxidants
Exposure to oxygen can expedite the aging process of plastics, leading to a decline in their strength, stiffness, and toughness. To prevent the breakage of molecular chains and prolong the product’s longevity, the inclusion of antioxidants is essential.
2. Impact Modifier
Impact modifiers are the key players in polymer manufacturing industries alike as an additive created to enhance a material’s resistance to impact and shock. This would allow it to support the material from breaking upon shock or impact of some kind. One can imagine how important this would be in almost any industry, including construction, automotive, and electronics.
3. Anti-Dripping Agent (Flame Retardant)
In any situation prioritizing fire safety, the focus is directed towards flame retardants and anti-dripping agents. These additives play a crucial role in preventing melted plastic from dripping onto the floor when exposed to high temperatures, notably reducing the risk of fire. Their significance is particularly pronounced in safety-focused sectors like electronics and home appliances manufacturing.
4. Anti-Static Agent
In environments where static electricity can pose a risk, anti-static agents are used to reduce the build-up of electrostatic charges. These polymer additives find application in the electronics and packaging industries, where protecting sensitive components or preventing dust attraction is crucial.
5. Colorant
Colorants are functional additives that bring vibrancy to plastic materials. They provide an extensive range of color options for aesthetics and branding, making them indispensable in the production of consumer goods, packaging, and various decorative items.
6. Other Additives
The world of functional additives is vast and diverse, with a range of other specialized additives like UV stabilizers, plasticizers, and nucleating agents, each serving a unique purpose in enhancing polymer properties.
Shine Polymer – Where Excellence Meets Innovation
It’s imperative to mention Shine Polymer, a pioneering company that has etched its name in polymer additive manufacturing. With a rich history and a sterling reputation, Shine Polymer has been at the forefront of developing and supplying high-quality polymer additives for decades.
Shine Polymer’s product offerings span a wide spectrum, including impact modifiers, anti-dripping agents, and polymer processing aids. What sets Shine Polymer apart are its three distinct advantages:
Reliable Products
Shine Polymer is renowned for its expertise. They have complete inspection methods for raw materials and finished products, ensuring that manufacturers can rely on their materials to meet and exceed performance standards.
Competitive Price
Shine Polymer provides value without compromise, offering cost-effective solutions that don’t compromise on quality. This makes their products accessible to various industries.
Exceptional After-Sales Services
Shine Polymer doesn’t just stop at providing top-tier additives. The company is committed to supporting its customers, offering exceptional after-sales services such as masterbatch quality analysis and on-site guidance.
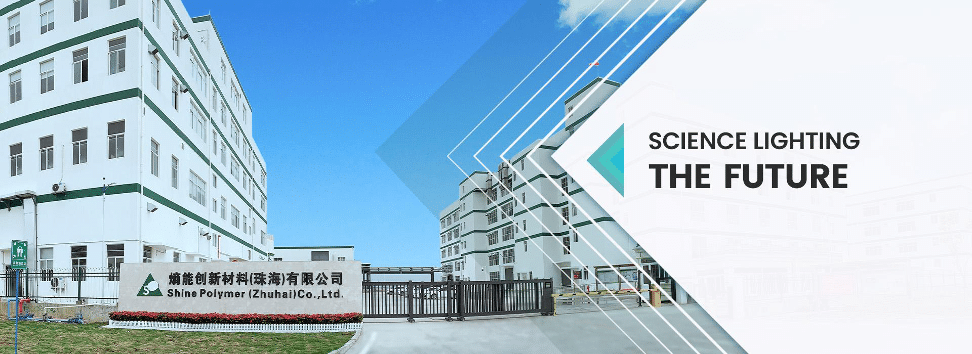
Unleash the Potential with Shine Polymer
It becomes evident that these remarkable compounds are the building blocks of innovation and excellence in the plastic industry. Shine Polymer stands as a testament to the commitment of companies dedicated to advancing this field. With a diverse range of reliable products, competitive pricing, and unparalleled after-sales services, Shine Polymer beckons readers to delve deeper into the world of polymer additives and uncover the endless possibilities they hold for the future. Unleash the potential with Shine Polymer and discover how innovation and excellence can transform the world of plastics.